Hydraulic Actuators:
A hydraulic actuator consists of a cylinder or fluid motor that uses hydraulic power to facilitate mechanical operation. The mechanical motion gives an output in terms of linear, rotary or oscillatory motion. Because liquids are nearly impossible to compress, a hydraulic actuator can exert considerable force. The hydraulic cylinder consists of a hollow cylindrical tube along which a piston can slide.
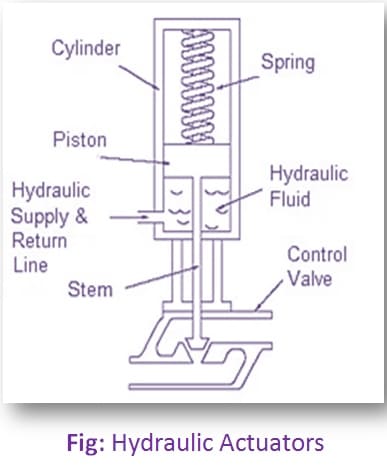
Advantages of Hydraulic Actuators:
1. Hydraulic actuators are rugged and suited for high-force applications. They can produce force 25 times greater than pneumatic cylinders of equal size. They also operate in pressure of up to 4000 psi.
2. Hydraulic motors have high horsepower-to-weight ratio by 1-2 hp/lb greater than a pneumatic motor.
3. A hydraulic actuator can hold force and torque constant without the pump supplying more fluid or pressure due to the incompressibility of fluids.
4. Hydraulic actuators can have their pumps and motors located a considerable distance away with minimal loss of power.
5. Hydraulics will leak fluid. Like Pneumatic actuators, loss of fluid leads to less efficiency. However, hydraulic fluid leaks lead to cleanliness problems and potential damage to surrounding components and areas.
6. It require many companion parts, including a fluid reservoir, motors, pumps, release valves and heat ex-changers along with noise-reduction equipment. This makes for linear motions systems that are large and difficult to accommodate.
Disadvantages of Hydraulic Actuators:
1. Fluids will leak and hence will deliver less efficiency.
2. Moreover leakage leads to cleanliness issues and potential damage to surrounding components and areas.
3. Hydraulic actuators need many additional parts which include fluid reservoir, motors, pumps, valves, heat exchangers, noise reduction equipment etc.
4. The overall weight of the system is very high.